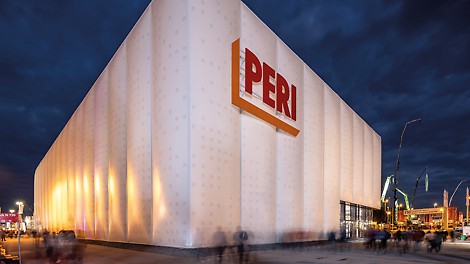
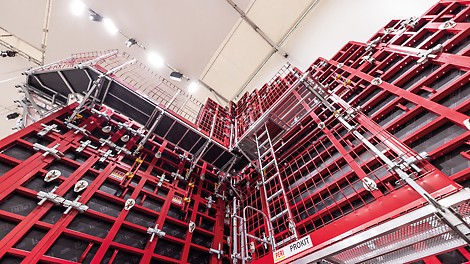
Download Press Release
The images in more detail
In what proved to be another highlight of this year’s bauma trade fair, PERI’s exhibition area was extended to include an additional stand in the outdoor area, which was dedicated exclusively to 3D Construction Printing. And right alongside PERI’s 3D construction printing stand was schaltec GmbH, a member of the PERI Group. In addition to formwork refurbishment and the supply of ready-to-install replacement formlining, the portfolio offered by schaltec GmbH in Germany includes value assessment and second-hand trading in formwork, scaffolding systems and associated components.
One 3D-printed tiny house for each day of the fair
Since the last bauma trade fair, PERI’s portfolio of 3D Construction Printing solutions has continued to evolve. The scope and size of the 3D-printed property was completely unrivalled at the trade fair: Visitors were able to watch on as the experts from PERI printed a new tiny house in Munich each and every day. The printer was running all day – from the beginning of the fair until the exhibition centre finally closed its doors. This enabled the 3D construction printing experts to impressively demonstrate how quickly a house can be printed. In addition, the construction printing experts presented a comprehensive portfolio of solutions that includes not only the provision of the 3D construction printer and sensor solutions, but also customer assistance services for the planning, approval and ultimately the realisation of printing projects. In printing technology, PERI relies on the COBOD BOD2 gantry printer from the Danish manufacturer and market leader COBOD, in which PERI has held a stake since 2018.
With the innovative MESH technology, PERI also had another highlight up its sleeve for architecture enthusiasts: This digital construction method makes it possible to produce reinforcement cages by way of an automated prefabrication process. The 3D grid structure created in this way then serves as formwork and reinforcement at the same time and is filled with a specific concrete mix. This allows complex shapes and structures to be created cost-effectively without conventional formwork and without formwork waste. The robot-assisted technology was developed at ETH Zurich and has been used in an industrial construction process in partnership with PERI and Sika since 2018.
Key technologies for digital construction sites
PERI can look back on countless lively and exciting discussions in the “Digital Base” of the exhibition hall. The portfolio of key digital technologies on show impressively illustrated how digitalisation is helping to accelerate progress on the construction site. The solutions are already increasing planning efficiency, safety and speed on the construction site to a significant degree. Among other things, visitors had the opportunity to familiarise themselves with the new myPERI Customer Portal, a variety of digital planning solutions, the range of sensors from PERI InSite Construction with its new ISC Hub, as well as numerous PERI apps. Moreover, PERI is also focusing on collaborations with start-ups, such as Scaled Robotics and Cosuno, and presented further trends and visions for the construction site of the future. This meant that promising start-up business models with impressive product demonstrations were given just as much of a platform in the PERI exhibition hall as tried-and-tested PERI products and services.
The PERI XR Ecosystem was of particular interest to the visitors. With the PERI Extended Experience App, PERI is taking the mobile 3D visualisation of formwork and scaffolding projects to a new level, optimising communication, safety and efficiency on the construction site. Thanks to Augmented and Virtual Reality, the virtual world and real life began to merge in Munich. Using the example of a scaffolding construction site, the project was projected into the physical environment together with the 3D model. This enables the workers on the construction site and the project managers in the office to communicate effectively with each other. The project managers are able to walk around the construction site in a virtual manner no matter their location, identify potential problems and ensure that the assembly process is carried out properly according to the model.
New formwork system for straightforward construction in slums
In cooperation with “Start Somewhere gemeinnützige GmbH”, PERI has set itself the goal of sustainably improving living conditions in slums. At bauma, the TwistBlock Moulds formwork system co-developed by PERI was showcased, a system that won the German Innovation Award 2021 in the “Building & Elements” category. With TwistBlock Moulds, residents are given the ability to make their own building materials in the form of hollow concrete blocks, thereby enabling them to create better housing on their own. TwistBlocks are handmade hollow concrete blocks that constitute a versatile, reusable, cost-effective and fire-safe building system designed specifically for slums. Thanks to this formwork system, the hollow concrete blocks can be produced manually by the slum dwellers themselves using the simplest of means and result in a modular, mortarless plug-in system that is up to 80 % reusable and can be erected and dismantled by hand. The blocks can be placed at any desired angle, without angle steps, in order to make maximum use of the plots in the slum, which usually have uneven surfaces. In future, the hollow concrete blocks will be produced by the slum dwellers themselves within small factories. Jobs and a construction industry are created directly on site, so that a large part of the value creation takes place in the slum.
In the first pilot project, the construction of a school building in the Kibera slum in Nairobi/Kenya, a complete building has been successfully completed using the TwistBlock system for the first time ever. The school was planned by architect Oliver von Malm, founder of “Start Somewhere gGmbH”. For the construction of the new “Oloo’s Children Centre”, 7,200 blocks were produced on site in the company’s own concrete block factory. The school has space for 400 children, who are now being taught there. As part of the sustainability programme, PERI assists with the construction of a new school every year.
Greater sustainability and efficiency for MAXIMO
The topic of sustainability was also addressed for tried-and-tested products, such as the MAXIMO Panel Formwork. The experts from PERI provided insight into the future of the tried-and-tested formwork, which is impressive in terms of efficiency and sustainability. The facelift involves optimising the sturdiness of the frame as well as adding an innovative and sustainable surface coating to the panels, which will increase their lifespan. Something else that is unique in the world of construction is the symbiosis between formwork and scaffolding from a single source: Thanks to the new functional brace, it will be possible to connect MAXIMO to the PERI UP Scaffolding Kit in a gridless manner, opening up new and efficient ways of accessing the formwork. The PERI RFID solutions that are built into the improved MAXIMO system optimise formwork deployment and logistics processes. Users are able to clearly identify and allocate the panels by scanning this RFID tag. Thanks to the RFID tags, it is also possible to call up specific component information, Instructions for Assembly and Use, and product videos digitally in the PERI MATERIAL SCAN App.
Innovations in the scaffolding sector
The PERI exhibition hall also featured completely new innovations for the scaffolding trade. These included a flexible enclosure system that is an ideal addition to the PERI UP Scaffolding Kit. With PERI UP Cladding, the scaffold can be enclosed quickly, providing the answer to the ever-increasing demands for weather and environmental protection on construction sites and the need for an attractive external appearance during building refurbishment. The virtually crevice-free enclosure system offers increased protection for site personnel, as it protects against driving rain and strong sunlight, for example, and also minimises the feeling of height. At the same time, it is sufficiently translucent to create a bright working environment in daylight.
The STS 300 Scaffold Transport System is also a new addition to the portfolio. Visitors to the PERI exhibition hall were able to experience first-hand how the transport system with removable and stackable baskets optimises working procedures for scaffolding projects.
Outlook: Turning visions into market-ready products
As always, once bauma has drawn to a close, all the attention turns to the next bauma trade fair. PERI is already working on optimising the existing product and service portfolio with further additions to make the world’s construction sites even safer, faster and more economical. Interested parties can look forward to seeing some of the concepts and visions presented this year as market-ready solutions at the next bauma trade fair.