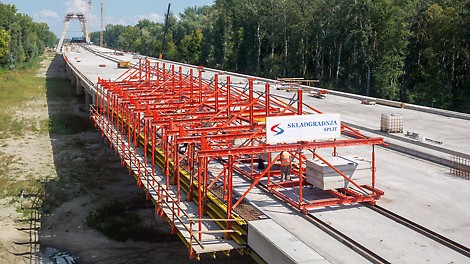
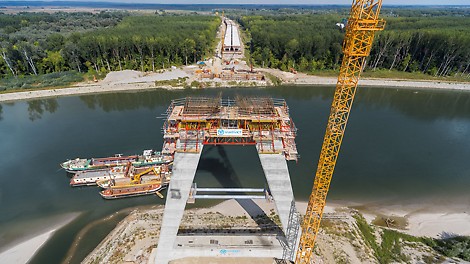
Download Press Release
The images in more detail
The 2,500 m long structure features two separate carriageways and consists of one cable-stayed bridge along with directly connected approach bridges. Two A shaped pylons carry the three main sections directly above the river with 100 m and 220 m spans respectively whose roadways are being realised using a steel composite construction method. The approx. 1,000 m long foreshore bridges on both sides are located in the flood area of the Drava river and are being realized with pre-stressed prefabricated beams on massive circular columns.
Responsible for the construction of the pylons is Viadukt dd from Zagreb whilst Split-based Skladgradnja d.o.o. is realizing the superstructure. Both construction companies are relying on in the planning and delivery of the Peri formwork solution – and respectively place very different requirements on the solution.
Reliable, fast solutions for columns and parapets
The adjacent beam bridges which span the flood area of the River Drava reach a length of around 1 km. The sections have regular spans of 35 m with six precast beams forming the two 13.50 m wide carriageways in each case. The 182 cm high pre-stressed concrete beams are in part produced on site in a field factory. With the individually designed formwork – consisting primarily of the proven GT 24 formwork girders and SLS spindles – the construction team requires only one working day per structural component. Loads from the bridge segments are transferred via the transverse beams into massive circular columns with 180 cm diameters and mushroom shaped enlargements. The special steel formwork from Peri for the columns facilitates rapid concreting and simultaneously ensures the best surface results.
For realizing the parapets on the external as well as internal areas of the carriageways, the Peri team developed a number of solutions based on the Variokit engineering construction kit. A cantilevered parapet carriage is being used for the large-sized cantilevered parapets on the outer edges, with dimensions of 80 cm x 35 cm, which can be moved very quickly. Anchorage to the structure is not necessary as the horizontal forces are transferred by means of friction – this makes the solution very cost effective and saves on any additional time and effort. The cantilevered parapets on the opposite side located on the inner side of the carriageway are formed using an ingenious combination of system components taken from the Variokit engineering construction kit and the Peri Up modular scaffold: the formwork constructions of both parapets are suspended on a spindle, and the loads are transferred via a laterally arranged RCS rail positioned above the carriageway into the Peri Up shoring towers. By means of simple rollers, this 36 m long construction can be quickly moved to the next concreting section in each case.
With these solutions for the construction of the cantilevered parapets, Peri fully complies with construction work requirements that places great importance on quick and simple handling, an absolute minimum of individual components and a high level of cost-effectiveness. Thus, after a short period of familiarization, the construction team has been able to achieve a 2 day cycle per section for the central parapets.
Climbing formwork systems for the pylons optimally combined
Two very striking, 75 m high A pylons with constantly changing cross sections will characterize the cable stayed bridge after completion. They form the suspension for the three bridge segments directly above the river and each carry the 100 m long external span as well as 110 m of the middle bridge section.
The Trio panel formwork provides the form for the up to 4.50 m thick foundations of the four pylon legs whilst efficiently transferring the fresh concrete loads of the 22 m x 22 m sub-structure. The rectangular cross-section of the towering pylons is constantly changing – from 6.50 m x 3.50 m in the base area up to 4.00 m x 5.00 m below the converging pylon head. For the construction of this complex geometry, Peri has combined CB climbing formwork and the RCS rail climbing formwork.
CB 240 climbing formwork complete with formwork carriage is being used on the front sides of the pylons, and a crane moves the units consisting of brackets and Vario GT 24 girder wall formwork from one concreting section to the next. The brackets are tilted by 8° to the vertical; thus the formwork follows the A shaped inclination of the front sides. For the forward and reversed-inclined outer surfaces of the pylon legs, the rail-guided RCS climbing formwork provides the optimal solution. By means of mobile hydraulic pumps, the units can continuously climb regardless of the weather and without requiring a crane. The climbing rails follow the constantly changing inclination of the pylon legs with angles of 16° on the inside and 18° on the outer side respectively. The fact that the working platforms can be adapted to suit the inclinations and are thus always in a horizontal position guarantees faster and safer working. Formworking operations have also been accelerated as a result of ensuring that during the planning of pre-fabricated Vario GT 24 wall formwork elements for the 60 cm thick pylon walls, only a minimum of modification work was required.
With the help of the overall concept for the pylons, the construction team is able to complete each of the 24 concreting sections within an average of 5 days – largely crane-independent and irrespective of wind and weather.
Positioned at a height of around 8 m, the reinforcing cross connection for the two pylon legs is formed using the Multiflex slab and Trio wall formwork systems. Peri Up Rosett Flex shoring towers carry the high loads into the ground. In the upper pylon area where the two legs converge to form a massive head section, a strong lattice framework comprised of components taken from the Variokit engineering construction kit serves as a safe working platform as well as as load bearing scaffold.
The new A5 motorway – part of the European corridor
The "Autocesta A5" (Croatian for the A5 motorway), also known as the Slavonika, is a highway in the eastern part of Croatia which is still under construction in part. When construction is finally completed, the A5 will connect the towns of Branjin on the Hungarian border and Svilaj on the Bosnian-Herzegovinian border. Near to Osijek, the motorway crosses the River Drava – with around 750 km, it is the fourth-longest tributary of the Danube.