
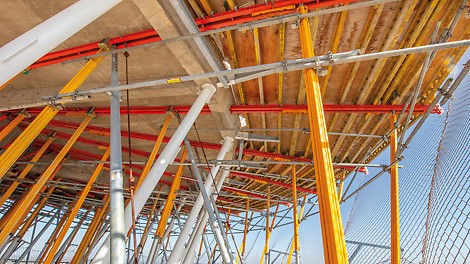
Download Press Release
The images in more detail
The Aeropuerto de Ezeiza is situated around two kilometres east of the city of Ezeiza, in the heart of the Argentinian province of Buenos Aires. It is where international flights from and to Buenos Aires take off and land. The new air traffic control tower for the runways, the platforms and the taxiways were built in close cooperation with PERI.
Unusual pipe-in-pipe structure
The construction phase of the project was extremely complex. In addition to forming a flawless surface in compliance with architectural concrete standards, an unusual geometric shape needed to be created. This would see two partition walls with a vertical pipe-in-pipe structure in the area of the shaft support the weight of the crown of the tower, which would house the air traffic control centre. The design would also see the central internal pipe house the stairwell, the lifts and the installation ducts. The elliptically shaped visible external pipe would be connected to the internal pipe by means of transverse partition walls. All in all, the tower would have 27 levels. Once the ceiling of the highest level was in place, the structure would stand at a height of 80.05 m. Once the steel roof and the antenna were in place, the overall height of the building would be 108.40 m.
Complex requirements for PERI engineers
The internal core of the tower extends vertically upwards. Therefore, the construction site team opted for a combination of the CB Climbing System and the VARIO GT 24 Girder Wall Formwork, which impressed on account of their continuously adjustable panel connections and facilitated flexible adjustments to accommodate project-specific requirements. The VARIO Formwork climbed upwards on the CB 160 while the work was being carried out on the external section of the wall. In the internal section, the BR Shaft Platform was used to provide reliable support for the internal formwork of the shaft.
To achieve the desired shape for the external pipe, an extensive amount of preliminary planning had to be carried out by the PERI engineers. This is because the geometry of the outer core changes from one level to the next from level five upwards. In practice, this meant that a three-dimensional planning model had to be custom-made and PERI special formwork had to be manufactured.
CNC cutting and special assemblies
What came out of this was a total of eight types of VARIO formwork in the form of VARIO 3D boxes – five of them for the external wall formwork and three for the internal wall formwork. The timber panels were cut with millimetre precision to meet the project requirements using the CNC service that is included in the PERI portfolio. On account of the metal and timber beams, which catered for both the curvature and the contact surface of the formwork, it was possible to re-adjust the panels in each set to accommodate the variable geometry of each level. This paved the way for a swift two-week concreting cycle.
Before work got underway at the construction site in Argentina, the viability of the concept was verified, i.e. the custom-made special components and all procedures were subjected to rigorous in-house testing by PERI engineers ahead of time. As such, the construction work was carried out twice, thereby maximising the safety of the construction site personnel.
The crowning glory
The air traffic control centre, the crown of the tower, was to be built at a height of around 62.00 m. This consisted of five cantilevered slabs, which, on account of their varying geometries, were installed using a number of different solutions. The MULTIFLEX Girder Slab Formwork was used on each of the five levels in combination with and supplemented by components of either the VARIOKIT Engineering Construction Kit, PERI UP Flex Shoring Towers, MULTIPROP Aluminium Slab Props and PEP Ergo Slab Props.
Radially suspended PERI UP Flex Working Platforms supported by parts of the VARIOKIT Engineering Construction Kit and making use of the Brace Frame SB-2 were used both as formwork support for the walls and hollow box girders, which were formed using VARIO 3D boxes, as well as support for the cantilevered slabs.
PERI UP Flex Working Platforms were also used to assist with the installation of the steel roof and the tower antenna at a height of 80.05 m. After all, the platform system’s ability to adapt flexibly to the geometry of the building is not its only stand-out feature – its non-slip steel deck and integrated lift-off protection also provided a high degree of safety at great heights. MULTIPROP Aluminium Slab Props combined with Steel Walers SRU were installed for the purpose of extending and supporting the platforms in a cantilevered manner, in a similar way to the work performed around the control centre.
Working together to reach objectives
PERI supervisors were on hand to train and advise the construction site personnel from the word go. Close collaboration between PERI and the client was a fundamental requirement over the course of the entire project, but particularly during the final phase of construction. This was the way to guarantee that the major project was executed smoothly and the tailor-made special-purpose solutions were implemented flawlessly.