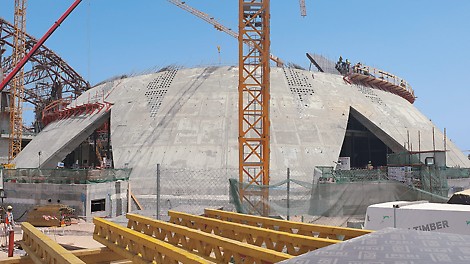
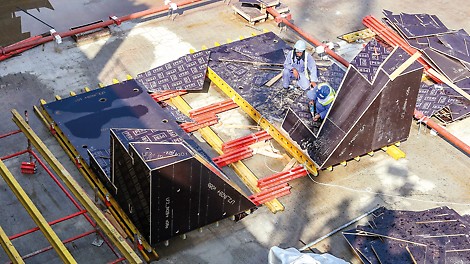
Download Press Release
The images in more detail
The SAAF is part of the new campus of Kuwait University whose plans were developed back in 2004. Upon completion, the new campus will bring together all 16 faculties of the university and its 40,000 students at one central location on an area covering 600 hectares. A total of seven different colleges will be accommodated on the area – from the College of Art and College of Business through to the College of Architecture. Furthermore, students will have access to additional facilities such as the indoor tennis centre.
The facade of the 25 m high tennis centre was constructed using 8 concreting heights. For the later refinement of the thin reinforced concrete slab with Trencadis mosaics made of limestone, triangular recesses were taken into consideration for the construction. The recesses have been positioned at different heights of up to 11 m and have up to 120 circular openings with respective diameters of 20 cm. These form a fine net that allows the natural sunlight to pass through the subsequently integrated glass blocks into the interior of the tennis centre. As a result, the sports venue with its diameter of over 80 m will be illuminated in a unique way.
Customised realisation of a very individual design
In order to fulfil the vision of the Skidmore, Owings and Merrill (SOM) firm of architects, Gulf Consultants, Kuwait University and construction company Societe d'Enterprise & de Gestion (SEG Qatar) put their trust in the experience of PERI engineers gained in the area of free-form formwork. PERI engineers from the technical office of the PERI Group in Germany designed the 3D building models as well as 3D plans on the basis of the building plans. For constructing the complex, curved reinforced concrete walls with differently sized box-outs along with varying wall thicknesses between 20 cm and 30 cm, customised 3D special formwork elements were used. In the process, the statically load-bearing elements were based on the VARIO GT 24 Girder Wall Formwork. After site personnel had undergone comprehensive training under the watchful eye of a PERI supervisor, assembly of the 3D formwork units and individual elements was carried out directly on the construction site in accordance with the PERI assembly plans.
Multiple use of the PERI formwork solutions
Logistical challenges faced by the contractor included the tight space conditions, limited availability of crane times as well as timing difficulties regarding management of other work activities such as the installation of the spectator precast seating’s. As the shape of the curved walls repeated itself horizontally within a concreting height, it was possible to utilise the special formwork elements multiple times. This meant that it has been possible to use the same formwork elements up to four times with each concreting operation. This has reduced the construction costs and also saved valuable assembly time on the construction site.
Safely and cost-effectively combined with PERI UP
For the efficient realisation of the building´s shape with its demanding architectural requirements, the PERI formwork and shoring solutions were perfectly matched to each other. Through the continuous system grid of 25 cm or 50 cm as well as the possibility of combining with SRU Steel Walers taken from the VARIOKIT Engineering Construction Kit, the PERI UP Flex Modular Scaffolding System in the form of a load-bearing structure could be optimally adapted to accommodate the different geometries and loads of the free-form formwork. The shoring system was also used as a safe and stable working platform for the construction team.
Individual on-site project support
PERI supervisors supported the construction team for ensuring the efficient and safe handling of the PERI systems. A PERI project manager assisted the site management in facilitating strict adherence to the construction schedule and cost plan. He ensured the smooth flow of all processes and work activities in the area of formwork and scaffolding technology – especially regarding the delivery logistics. As a result, profitability of the project was not only ensured by the project-specific optimised use of the equipment but in particular by the constant supervision and adaptation of the material quantities on the jobsite. Importantly, all those processes involved in the planning and logistics along with the formwork assembly were precisely tracked and timed by the PERI project manager, and matched to the actual construction process down to the last detail.