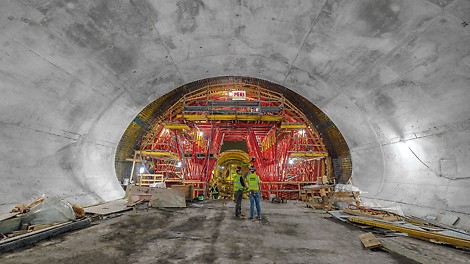
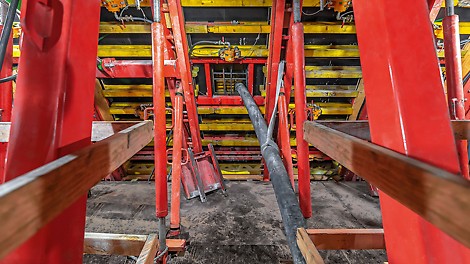
Download Press Release
The images in more detail
The highest point of the oval-shaped underground structure is still 17 m below Stockton Street which is why the construction using the cut-and cover method would have been too cumbersome and expensive. The contractor therefore decided in favour of shotcrete construction, also known as the New Austrian Tunnelling Method, in which excavation work takes place step-by-step from top to bottom. As more and more soft ground is excavated, temporary reinforcement provides support for the ever-increasing wall surface of the hollow space. Shotcrete applied to the surfaces supported the cavity until the inner lining could be cast in situ.
Project-specific VARIOKIT solution deep underground
The solution provided by PERI engineers for executing the enormous 60 m long Chinatown Station with a 15 m diameter stipulated concreting operations in 9 m sections. In order to be able to carry the large and heavy formwork ring, a project-specific formwork carriage consisting of high load-bearing VARIOKIT core components was realised. The pre-assembled formwork elements, comprised of GT 24 formwork girders and plywood formling, also saved weight when compared to using heavier steel formwork. These were lowered from Stockton Street through the site access to a depth of 30 metres and then mounted on the rail-guided VARIOKIT Tunnel Formwork Carriage. The hydraulic support of the VTC accelerated shuttering operations after the reinforcement had been placed in position. Concreting took place alternately on both sides in order to keep the supporting structure balanced. Vibrators mounted on the formwork could also be activated as required which ensured uniform compaction of the poured concrete.
Different cross-section – same supporting structure
Once the procedure had been established, the 9 m sections could then be concreted in five to six hours thanks to the high permissible fresh concrete pressure of up to 90 kN/m². After each concreting operation, striking was easily and quickly carried out by means of the hydraulic support. The tunnel formwork carriage was subsequently pulled along rails using heavy-duty wheels to the next section.
After the first ten concreting cycles, the tunnel profile changed. Due to the flexible VARIOKIT modular construction system complete with numerous rentable system components and the VTC Telescopic Prop, the supporting structure together with the other components were easily adapted in order to accommodate the new geometry. Once equipped with the new formwork elements, the final 10 sections could likewise be quickly realised thanks to the well-coordinated and practised procedures.
Individual formwork and logistics solution from a single source
The VARIOKIT modular construction kit is characterised by its great flexibility, high load-bearing capacity of its components and their low weight. The project-specific solution with prefabricated timber formwork panels delivered to the construction site as well as the large proportion of rentable system components provided the clients with enormous savings regarding investment, logistics and the amount of work involved. Due to the high adaptability of the system, numerous time-consuming and cost-intensive carpentry solutions could be dispensed with. Construction site support provided by the PERI project support team continuously optimised all work processes.