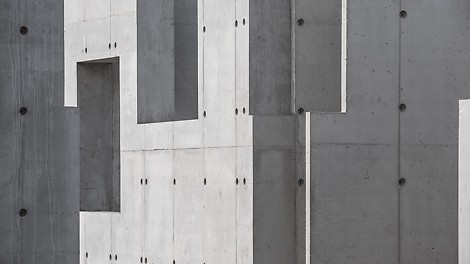
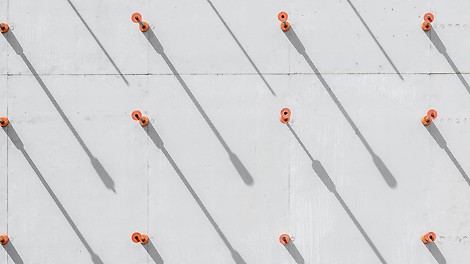
Download Press Release
The images in more detail
In many ways, the project disrupts traditional methods of construction, making them more efficient or convenient for labourers. The choice of formwork is one of the methods that challenges the norm in building methodology. The entire cast in-situ concrete structure has been formed using DUO, a technopolymer plastic formwork system, instead of traditional timber or heavy steelshuttering throughout. Normally, DUO would be used to form small regular-shaped structures as an efficient alternative to heavier systems, whereby the need for tools and highly skilled labourers would be reduced. This project was a great way to test DUO and see if the system was capable of more.
The pours in detail
PERI pushed the boundaries of what could be achieved with standard DUO panels. 355 panels were erected to construct the entire build, with each panel offering 30 to 35 reuses for a combination of horizontal and vertical applications. All walls were completed in 29 pours, with pour heights varying from 2.3 m to 3.8 m. ALPHA props provided direct support for 345 m² of concrete slabs, which were concreted in five pours. The customer also used DUO to pour 0.3 m and 1.4 m-high slab steps and upstand walls independent of technical drawings, demonstrating its ease of erection for simple structures.
DUO proves to be the right solution
From the onset, the idea was to use DUO panels for horizontal and vertical applications to form slabs, columns and walls. The lightweight panels, the largest weighing no more than 25 kg, were ideal for the project due to its location and confined site space. Labourers were able to lift and move the panels around the site by hand, eliminating the need for a crane to erect the system. Furthermore, DUO aligned with Adrian’s vision of reducing waste during construction. All of the raw material is 100% recyclable and can be reused in the production of new panels, making it a sustainable alternative to using conventional formwork on this project. The system also offered logistical benefits. Due to the weight of the panels, only three lorries were required to deliver material from PERI’s depot to the site.
Design work extends limitations
When visualising the geometry of a house, the shape of Concrete House is not one that usually springs to mind. Quite literally, the structure pushes the boundaries of a ‘simple square’, as it comprises irregular angles in addition to varying floor heights throughout. This was a new application for DUO, as the system is generally configured in perpendicular lines to construct regular shapes. PERI’s technical team had to control the balance between achieving the architect’s design requirements and ensuring that the arrangement of DUO shutters was compatible with the system’s limitations.
PERI solution integrated Resilia concrete
In addition to formwork design, seamless construction and a steady supply of concrete is crucial when achieving a consistent finish. Resilia is a fibre reinforced self-compacting concrete mix. Due to its fluidity, the concrete exerts a higher pressure than conventional concrete. Panels were limited to a maximum pressure of 50 kN per m². In order to work within these limitations, concrete had to be poured in a controlled manner, especially as this was a unique mix that had never been used with the system and formlining before. The consistency of the mix enabled concrete to flow naturally into the complex formwork shapes, without requiring vibration. Although self-compacting concrete has a high flow rate, delays in the concreting process can affect the finish as the mix starts to solidify. Regular deliveries from a local production site reduced the chances of this occurring on the project. This was complemented by the fact that the number of DUO shutters erected on site justified the volume of concrete delivered for each pour. Overall, the concrete mix and formwork worked well together to create the bold and unique finish that was desired.